OEM Manufacturer Standing Seam Roll Forming Machine - rain gutter forming machine – Xinnuo Detail:
*Detail
Rain Gutter equipment is the production of building roof gutter roll forming machine, the production of gutter refers to the building roof between the two hip concave part, used for house drainage.
Xinnuo Gutter roll forming machine is designed with a dimension of 8.2 *1.3*1.5m. It is distinguished for stable performance, high price/performance ratio, and easy operation. The gutter roll former in Xinnuo has been certified by CE. ISO, and TUV
Xinnuo has been developing and producing cold roll forming equipment since 1998. We are competent in customizing roll formers for clients according to their specific requirements and applications.
*Model:90type Rain gutter
Configurations | Manual Uncoiler ,Guiding Platform ,Coil Strip Leveler ,Main Machine Of Roll Forming ,Electro-Motor,Cutting Device ,Hydraulic Station ,PLC Control, Supporter Table. |
Control System | PLC Delta Inverter |
Main Frame | 350mm H-Beam |
Main Power | 4 kw |
Pump Power | 3 kw |
Power Supply | 380V, 3-Phase,50Hz |
Forming Speed | 8-16m/min |
Roll Station | 18-22 stands |
Roller Diameter | 70mm |
Hydraulic Pressure | 10-12MPa |
Forming Size | 90mm |
Feeding Thickness | 0.3-0.8mm |
Feeding Width | 160mm |
Backboard Thickness | 14mm |
Chain Size | 33mm |
Cutter Standard | Cr12 |
Roller Standard | Cr12 |
Cr-Plating Size | 0.05mm |
Overall Size | 8200×1000×1200mm |
Total Weight | 5T |
All technical parameters can be changed,according to user s need.
*Details Pictures
*Application
Product detail pictures:

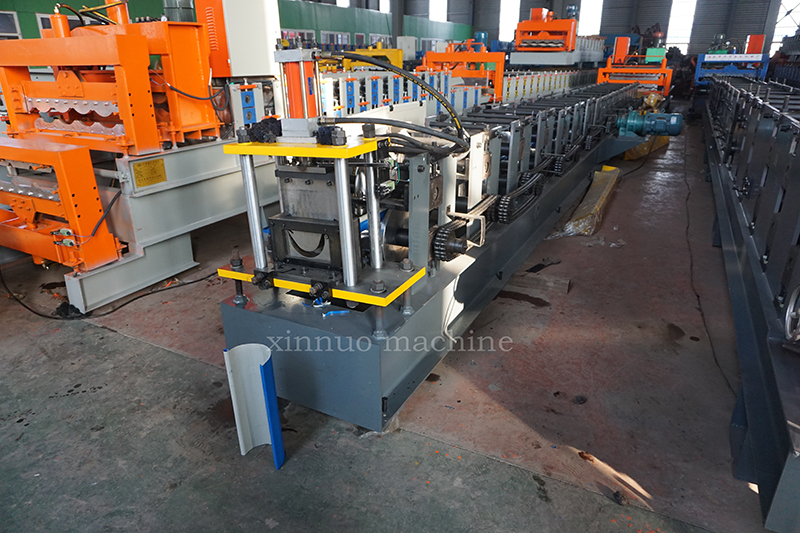
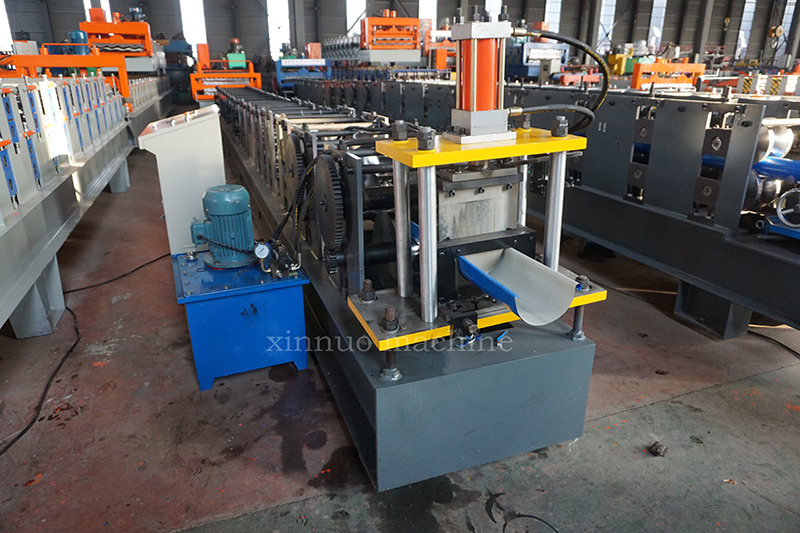

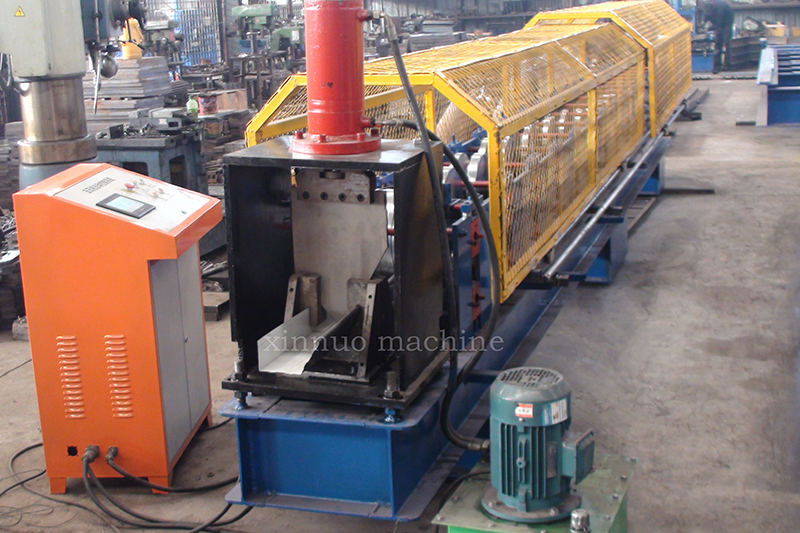
Related Product Guide:
Bear "Customer initially, High-quality first" in mind, we work closely with our prospects and supply them with efficient and specialist companies for OEM Manufacturer Standing Seam Roll Forming Machine - rain gutter forming machine – Xinnuo, The product will supply to all over the world, such as: Finland, Liberia, Korea, Now the competition in this field is very fierce; but we will still offer best quality, reasonable price and most considerate service in an endeavor to achieve win-win goal. "Change for the better!" is our slogan, which means "A better world is before us, so let's enjoy it!" Change for the better! Are you ready?
♦ COMPANY PROFILE:
Hebei Xinnuo Roll Forming Machine Co., Ltd., not only produce different types of professional roll forming machines, but also develop intelligent automatic roll forming production lines, C&Z shape purline machines, highway guardrail roll forming machine lines, sandwich panel production lines, decking forming machines, light keel machines, shutter slat door forming machines, downpipe machines, gutter machines, etc.
Advantages of Roll Forming A Metal Part
There are several advantages of using roll forming for your projects:
- The roll forming process allows operations such as punching, notching, and welding to be performed in-line. Labor cost and time for secondary operations are reduced or eliminated, reducing part costs.
- Roll form tooling allows for a high degree of flexibility. A single set of roll form tools will make almost any length of the same cross-section. Multiple sets of tools for varying length parts are not required.
- It can provide better dimensional control than other competing metal forming processes.
- Repeatability is inherent in the process, allowing easier assembly of roll formed parts into your finished product, and minimizing problems due to “standard” tolerance build up.
- Roll forming is typically a higher speed process.
- Roll forming offers customers a superior surface finish. This makes roll forming an excellent option for decorative stainless steel parts or for parts requiring a finish such as anodizing or powder coating. Also, texture or pattern can be rolled into the surface during forming.
- Roll forming utilizes material more efficiently than other competing processes.
- Roll formed shapes can be developed with thinner walls than competing processes
Roll forming is a continuous process which converts sheet metal into an engineered shape using consecutive sets of mated rolls, each of which makes only incremental changes in the form. The sum of these small changes in form is a complex profile.

The supplier abide the theory of "quality the basic, trust the first and management the advanced" so that they can ensure a reliable product quality and stable customers.

-
OEM manufacturer Downspout Roll Forming Machine...
-
Factory Cheap Hot Jupiter Roofing Machine - st...
-
Factory wholesale Used Roll Forming Machine For...
-
High-Quality Channel Rolling Machine Pricelist ...
-
Wholesale Purlin Making Machine Suppliers - c ...
-
Best Price on K Span Roll Forming Machine - Hi...