Oem Universal Bending Machine Factories - Hydraulic uncoiler – Xinnuo Detail:
*Detail
This roll forming machine produces roller shutter door with the roll forming technique in a synchronous forming manner. With computer control system, hydraulic shearing, and auto counting system, the production is conducted fully automatically. The roll forming system contributes to smooth and flat panel surface. Supported by an experienced design team, Xinnuo is competent in offering you efficient customization service. Any customization requirements upon panel’s width, thickness, and appearance will be met here.
*Features
a. The shearing speed of the roll former Is up to 10-16m/min. The upper roll can be corrected automatically so the system can still work well under high speed.
b. The shearing system is equipped with punching devices. The max allowable shearing thickness of the roll former is up to 1.2mm, while the shearing thickness of common machines is generally no more than 0.6mm.
C. Can be customized according to customer requirements
*Specification
Control System | PLC Colored Touch Screen |
Main Frame | 18mm steel welding |
Main Power | 3kw |
Pump power | 3kw |
Power Supply | 380V, 3-Phase,50Hz or any |
Forming Speed | 8-16m/min |
Roll Station | 14 stands |
Shaft Diameter | 50-70 mm |
Feeding Thickness | 0.3-1.2mm |
Cutter Standard | GCr12 |
Roller Standard | 45# Plating Cr |
*Details Pictures
*Application
Product detail pictures:
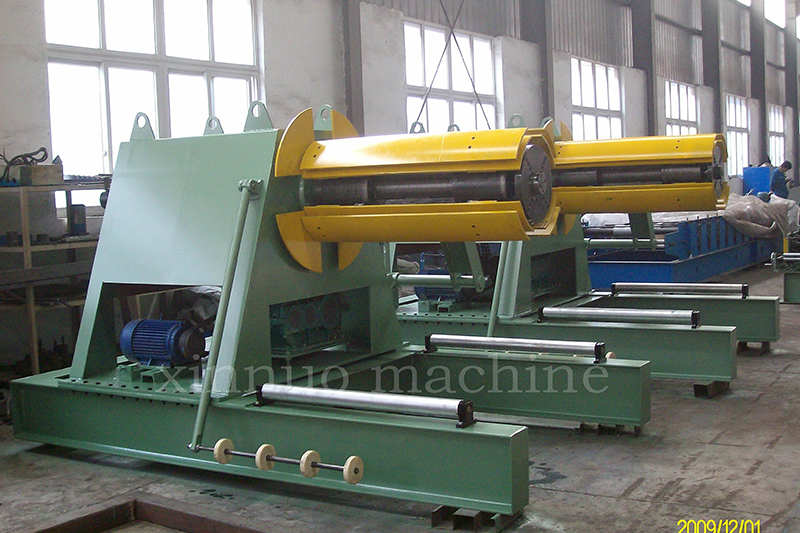
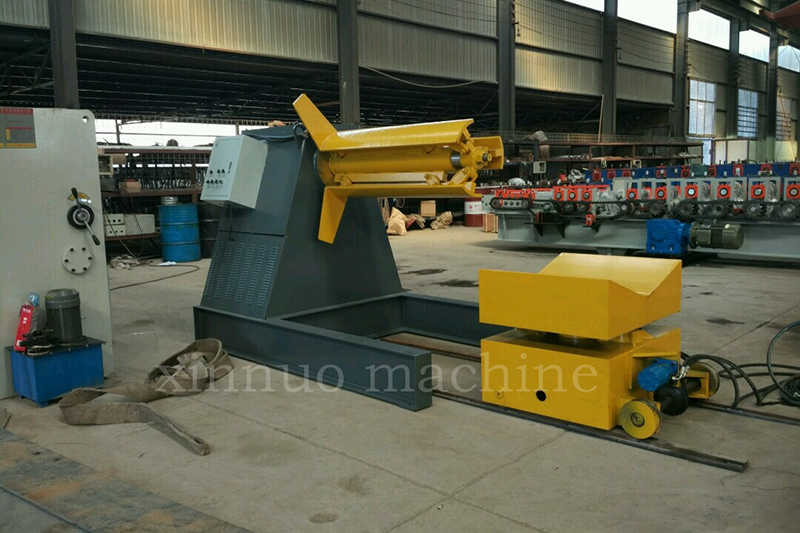




Related Product Guide:
Our development depends on the advanced equipment, excellent talents and continuously strengthened technology forces for Oem Universal Bending Machine Factories - Hydraulic uncoiler – Xinnuo, The product will supply to all over the world, such as: Swiss, Albania, Ireland, To let customers be more confident in us and get the most comfortable service, we run our company with honesty, sincerity and best quality . We firmly believe that it is our pleasure to help customers to run their business more successfully, and that our experienced advice and service can lead to more suitable choice for the customers.
♦ COMPANY PROFILE:
Hebei Xinnuo Roll Forming Machine Co., Ltd., not only produce different types of professional roll forming machines, but also develop intelligent automatic roll forming production lines, C&Z shape purline machines, highway guardrail roll forming machine lines, sandwich panel production lines, decking forming machines, light keel machines, shutter slat door forming machines, downpipe machines, gutter machines, etc.
Advantages of Roll Forming A Metal Part
There are several advantages of using roll forming for your projects:
- The roll forming process allows operations such as punching, notching, and welding to be performed in-line. Labor cost and time for secondary operations are reduced or eliminated, reducing part costs.
- Roll form tooling allows for a high degree of flexibility. A single set of roll form tools will make almost any length of the same cross-section. Multiple sets of tools for varying length parts are not required.
- It can provide better dimensional control than other competing metal forming processes.
- Repeatability is inherent in the process, allowing easier assembly of roll formed parts into your finished product, and minimizing problems due to “standard” tolerance build up.
- Roll forming is typically a higher speed process.
- Roll forming offers customers a superior surface finish. This makes roll forming an excellent option for decorative stainless steel parts or for parts requiring a finish such as anodizing or powder coating. Also, texture or pattern can be rolled into the surface during forming.
- Roll forming utilizes material more efficiently than other competing processes.
- Roll formed shapes can be developed with thinner walls than competing processes
Roll forming is a continuous process which converts sheet metal into an engineered shape using consecutive sets of mated rolls, each of which makes only incremental changes in the form. The sum of these small changes in form is a complex profile.

The product classification is very detailed that can be very accurate to meet our demand, a professional wholesaler.

-
Factory supplied Omega Shape Forming Machine -...
-
Wholesale Tile Roll Forming Machine Manufacture...
-
Best quality Tile Making Machinery - shutter d...
-
Oem Metal Sheet Forming Machine Suppliers - ra...
-
Wholesale Cold Roll Forming Machine - glazed t...
-
High-Quality Glazed Tile Roll Forming Machine F...